Where Is the Coatings Industry Headed?
The ECS 2025 made one thing clear: sustainability, functionality, and digitalization are no longer just trends — they are redefining how coatings are formulated and developed. At the heart of this transformation lies Material Intelligence — the integration of chemistry and data to enable smarter, faster innovation. In this blog post, we explore six key developments from the ECS that illustrate how the industry is embracing this shift.
The European Coatings Show (ECS) is much more than a trade fair — it’s considered a barometer of an industry in transition. The 2025 edition once again made this clear: three themes are shaping the evolution of the coatings sector — sustainability, functionality, and digital technologies. One thing became especially apparent: the way data is handled is transforming how coatings are developed, assessed, and optimised. The industry is increasingly moving toward what is now often referred to as Material Intelligence. We’ve summarised six key developments from the ECS 2025 that illustrate this shift — and show how they’re reshaping the industry’s understanding of formulation and innovation.
Sustainability Becomes a Prerequisite
Only a few years ago, sustainability was seen as a unique selling point for select suppliers. Today, it’s a prerequisite for many viable products — a trend clearly reflected in the ECS 2025 conference programme.
Many presentations focused on how to design more sustainable coatings: bio-based raw materials such as lignin, cottonseed oil or sugar alcohols were discussed alongside VOC-reduced water-based systems, PFAS-free additives, and alternative binders. The recyclability of materials was also a key topic — with new approaches to polyurea recovery and CNSL-based polyols gaining attention.
Across the talks and the four ECS halls, the message was unmistakable: sustainability is no longer a downstream optimisation — it’s a foundational aspect of formulation from the outset.
And this is exactly where digitalisation can make a crucial contribution. Anyone aiming for more sustainable formulations needs solid data — on raw materials, interactions, life cycles, and regulations. Digital tools have the potential to systematically unlock and apply this knowledge.
Functionality Is Becoming the New Standard
The demands placed on modern coatings go far beyond protection and appearance. Many recent developments focus on added functional properties — from self-cleaning or antimicrobial surfaces to UV protection, heat conductivity, or flame retardancy. New materials such as sol-gel coatings, core-shell nanoparticles, or self-initiating resins enable solutions that were previously difficult to implement.
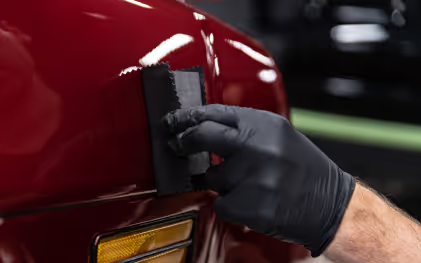
What used to be a niche application is becoming the norm: coatings are increasingly expected to contribute actively to the function of the end product — not just passively protect it.
As highlighted in a 2024 report by FARBE UND LACK, functional coatings are experiencing sustained global growth. Industry experts predict the market for functional paints will reach nearly €930 million by 2031, driven by growing demand in sectors such as automotive, construction, and aerospace.
Specialization Replaces Universality
In sectors like automotive, wood coatings, and construction, requirements are becoming increasingly differentiated — and formulation strategies are evolving in response.
"The era of “one-size-fits-all” solutions is over. Today’s companies increasingly rely on deep process understanding and create tailor-made systems aligned with the specific requirements of each application"
In automotive, coatings must now do more than look good: they need to be lightweight, scratch-resistant, UV-stable, and sustainable. The construction industry, on the other hand, is focusing on CO₂-reduced cementitious systems and coatings with enhanced insulation properties. Wood coatings require thixotropic, pumpable systems that ensure uniform application and high process stability.
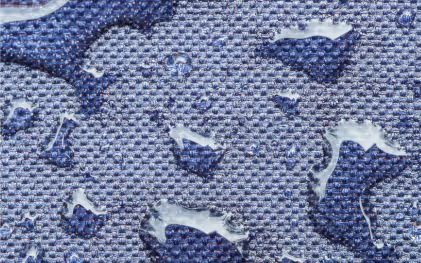
This trend is supported by digital technologies that enable faster adjustment and more flexible production. Advanced formulation and simulation tools allow new variants to be developed and adapted to specific requirements — turning complexity into a strategic advantage for manufacturers and customers alike.
The era of “one-size-fits-all” solutions is over. Today’s companies increasingly rely on deep process understanding and create tailor-made systems aligned with the specific requirements of each application — not only in terms of chemistry, but also regarding processing, durability, compliance, and sustainability.
Materials Science Remains Fundamental
Despite the momentum around digitalization, chemistry continues to form the foundation of innovation — a fact once again confirmed at ECS 2025. A wide range of new material concepts demonstrated the industry’s ongoing investment in raw material advancement: reactive surfactants, hybrid pigments, bio-based diluents, silicone-free defoamers, and novel esters for UV-curable systems received particular attention, alongside more complex binder structures and functional fillers.
The pressure to innovate is growing — especially where sustainability, processability, and performance must be balanced. And this is where materials science continues to deliver essential breakthroughs.
For example, Kuraray presented new polymers with ISCC PLUS certification — developed specifically for sustainable coatings and printing inks. ISCC PLUS is an internationally recognized certification system that verifies the sustainable origin and traceability of bio-based or circular feedstocks.
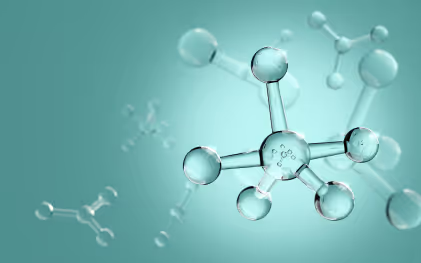
Hubergroup Chemicals also introduced UV-curable oligomers with up to 70% bio-based carbon content, offering performance levels comparable to conventional systems — but with significantly improved environmental credentials.
These developments continue a trend already visible in 2024, when trade media highlighted growing demand for functional, sustainable raw materials that not only meet regulatory standards but also offer genuine application benefits — from improved adhesion to more efficient curing.It’s clear: materials science remains the origin of new recipes — and the key to transforming challenges like resource conservation and regulatory compliance into market-ready solutions.
It’s clear: materials science remains the origin of new recipes — and the key to transforming challenges like resource conservation and regulatory compliance into market-ready solutions.
Regulation as a Driver of Innovation
Regulatory frameworks such as the CSRD (Corporate Sustainability Reporting Directive) and the ESPR (Ecodesign for Sustainable Products Regulation) are increasingly acting as innovation drivers within the coatings industry. Companies are no longer simply choosing to report on sustainability — they are now required to systematically account for environmental impact, resource efficiency, and circularity.
As a result, sustainability is no longer merely market-driven — it is being defined by regulation, and is already shaping product and formulation development. Anyone reporting on environmental performance must actively design for it.
At ECS 2025, many manufacturers demonstrated that they view regulatory requirements not as limitations, but as opportunities for innovation. New product concepts — such as PFAS-free additives, bio-based binders or energy-efficient curing systems — are being developed at the intersection of technical progress and compliance. Testing methods are also evolving, with new metrics for durability and recyclability gaining traction.
In short: Regulation is no longer just a directive — it’s an impulse. It provides direction, accelerates transformation, and fosters sustainable solutions that can compete on the market.
Digitalization and AI: Material Intelligence on the Rise
One of the most dynamic areas at ECS 2025 was the growing role of data, artificial intelligence (AI), and digital tools in product development. Across multiple presentations, it became clear: the industry is moving beyond trial-and-error and toward predictive, data-driven development processes. Examples included digital formulation assistants, machine learning models for recipe optimisation, and web-based tools to systematically plan experimental design.
At the heart of this movement is a new understanding of data — and with it, a concept gaining traction across the sector: Material Intelligence.
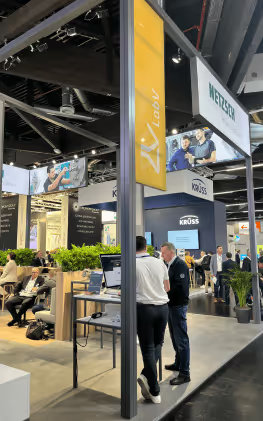
Material Intelligence refers to the ability to organise, connect, and analyse material data across processes and systems to generate actionable insights. It’s not just about collecting data — it’s about transforming it into a reliable basis for decisions: faster, more precise, and repeatable.
In practice, this means the properties of a formulation can be predicted before the first batch is mixed. Historical test data and performance results feed directly into the next optimisation. And teams across locations work from a shared, consistent data foundation.
Material Intelligence is changing not only how formulations are developed, but how knowledge is managed. It links chemical expertise with digital logic — and lays the groundwork for a new kind of development: more efficient, more sustainable, and more intelligent
Conclusion: A New Way of Thinking Across the Industry
ECS 2025 made it clear: the coatings industry is undergoing fundamental change — not only technologically, but in mindset. Sustainability, functionality, and digitalisation are no longer isolated trends — they are converging, reinforcing one another, and jointly shaping the future of formulation. Whether through bio-based raw materials, functional performance, or AI-driven development strategies — the expectations are rising, but so is the potential. The shift is underway: from standard solutions to application-specific, intelligent systems that balance environmental impact, performance, and process efficiency. Material Intelligence stands as a symbol for this transformation: a strategic synthesis of chemical insight and data-driven decision-making. Those who begin today to combine sustainable innovation with digital tools and functional value creation are not just adapting to the future of the industry — they are helping to shape it.
For more information on LabVs Material Intelligence Platform (MIP), please check out this page.